Flows with Chemical Reactions
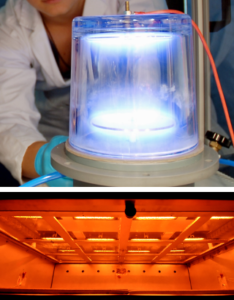
Research group B2 Flows with Chemical Reactions – Combustion Technology was established as a part of LSTM in 1996. Research conducted by the B2 group is strongly application oriented and includes experimental research of flows with chemical reactions, as well as heat and mass transfer processes, all supported through virtual engineering and numerical simulations (CFD).
The most technically important representative of flows with chemical reactions are combustion processes, which represent the main research area of the B2 group. Different technologies have been developed here, from initial research to their technical implementation. The so-called volumetric ceramic burner technology (also known as porous burner technology) was developed at LSTM, it has been continuously optimized and adapted to a wide variety of applications, including steel, glass and food industry. Other important research point is investigation of non-thermal plasma, e.g. for water remediation and surface cleaning.
-
Entwicklung eines neuartigen Grundwassersanierungsverfahrens zur Beseitigung niedrig konzentrierter perfluorierter Tenside und ihrer Präkursoren mittels Behandlung durch Adsorption und nichtthermischem Plasma Delgado
(Third Party Funds Single)
Term: 1. February 2020 - 31. January 2022
Funding source: Bundesministerium für Wirtschaft und Technologie (BMWi)Das Projekt zielt auf eine neuartige Wassersanierungsmethode zur Beseitigung perfluorierter Tenside (PFT) aus Grund- und Abwasser mit einem deutlich höheren Wirkungsgrad als bisher erreichbar. PFT sind Organofluorverbindungen, die aufgrund ihrer Bioakkumulation und schlechten Abbaubarkeit in der Umwelt sowie wegen ihrer negativen Auswirkungen auf die menschliche Gesundheit bedenklich sind. In der Öffentlichkeit wurde man zunehmend auf PFT aufmerksam, daher bietet eine geeignete Wassersanierungsmethode einzigartige Marktchancen.
Die Möglichkeiten zur Beseitigung von PFT aus kontaminierten Gewässern sind aufgrund ihrer extremen chemischen Stabilität begrenzt. Die Hauptbehandlungsmethode ist die Adsorption mittels Aktivkohle, was aber mit hohen Betriebskosten verbunden ist. Die vorgeschlagene Methode besteht aus einer nicht-thermischen atmosphärischen Plasmabehandlung, bei der der Hauptanteil an PFT zersetzt wird, sowie der Adsorption durch Ionenaustauscher, bei der der Restanteil an PFT adsorbiert wird. Hierbei dienen numerische und experimentelle Untersuchungen sowie Dauertests an einem Testfeld zur Verifikation und Charakterisierung des neuartigen Wassersanierungskonzepts.
-
LOHCmobil - H2 Verbrenner/ Konstruktion und Erprobung des volumetrischen keramischen Brenners
(Third Party Funds Single)
Term: 1. January 2018 - 31. December 2020
Funding source: Bundesministerium für Wirtschaft und Technologie (BMWi)Das Ziel des Projekts ist die Entwicklung eines deutlich kompakteren und dynamischeren Wasserstoff-Freisetzungsverfahrens auf Basis eines volumetrisch-keramischen Brenners mit entsprechendem Kesselsystem zum Einsatz in stationären und mobilen Wasserstofffreisetzungsanlagen und dessen allgemeingültige effiziente Integration und Anpassung in diese Anlagen, um die Kommerzialisierung der Wasserstoffspeicherung in LOHC im Markt voran zu treiben. Das neue Verfahren soll den Eigenverbrauch an Wasserstoff für die Verbrennung bei einer 100 kW Wasserstofffreisetzungsanlage von derzeit etwa 45 kW auf insgesamt angestrebte 30 kW reduzieren. Zudem soll das neue Verfahren deutlich kompakter und dynamischer sein als derzeit auf dem Markt vorhandene Brennersysteme. Die ermöglichten, schnellen Lastwechsel sollen die Integration in mobile Anwendungen ermöglichen.
-
Systematische Untersuchungen zur Einsatzqualifizierung einer innovativen Backofentechnik mit volumetrischem keramischem Brenner (VKB) einstellbaren Wellenlängenspektrums sowie hoher Regeldynamik und Energieeffizienz
(Third Party Funds Single)
Term: 1. May 2014 - 30. April 2017
Funding source: AIF Arbeitsgemeinschaft industrieller ForschungsvereinigungenAs part of thisresearch project, a possibility of application of a novel gas-fired baking oventechnology is to be developed, in which for the first time in the food industrya volumetric ceramic burner (VCB) is to be used. In many other industrialfields, VCB systems have demonstrated superior energy utilization and processecology. A VCB-based baking oven technology combines the benefits of energytransfer, primarily due to thermal radiation, with a broad power modulationrange. Thus, it promises not only the possibility of influencing the wavelengthspectrum and its radiation intensity, but also an otherwise unattainablecontrol dynamics, which is needed for the design and implementation of variousbaking programs, and the resulting increased energy efficiency. A VCB-based gas-firedbaking oven technology therefore offers particular advantages to small andmedium-sized enterprises (SMEs), which frequently vary their product range and productioncapacities.
The baking oven type, the design of the thermal energy supply system, themoisture content in the baking oven and the baking time have a decisive effecton the resulting mass and energy transport conditions. However, there is a lackof knowledge about required optimal process conditions. Experimental studieshave shown the positive influence of thermal radiation on the baking process, e.g.reduction of energy required for the baking process and improvement of transferredthermal energy control and regulation. In this regard, there are so farinsufficient data regarding the optimal wavelength range for baking purposes.
The aim of this research project is development and operational qualificationfor a novel gas-fired baking oven concept based on a volumetric ceramic burner.Potential for application of this technology requires a critical evaluation ofthe operating window in interaction with product properties and processparameters. An additional goal is to explore which process conditions can berealized in the novel gas-fired furnace through the specific use of theinnovation-bearing characteristics, its control and wide dynamic powermodulation range and increased energy efficiency. The interdisciplinary projectis intended to create the basis for a fast and broad transfer of an innovativebaking technology and is thus of relevance to both companies in the field of bakingoven construction and users in the baking industry. In particular, SMEs willbenefit from the results, as their competitiveness can be increased by costsavings of 20 to 30% of energy costs for baking processes.
Topics, currently or previously addressed in projects, include:
- burners and combustion systems,
- porous volumetric ceramic burner technology,
- combustion of hydrogen and of low calorific gases,
- heating systems,
- industrial combustion units,
- biomass gasification,
- drying facilities,
- steam generators,
- thermal energy recovery from exhaust gases,
- flue gas treatment,
- fuel cells,
- hot jets,
- non-thermal (cold) plasma applications,
- wastewater treatment,
- investigation of high-temperature resistant ceramics,
- numerical simulations of flows and of combustion processes,
- development of sensors and measurement systems, etc.
Experimental facilities:
- Five laboratories for the experimental research, including three bunker laboratories,
- Three gas analyzers (for O2, CH4, CO2, CO, NO, NOx, etc.)
- FID – analyzer (C3 equivalent)
- Thermography system (50 Hz)
- IR Color (Dual frequency) Pyrometer
- 16 long-term test setups for burners (24/7 use)
- High temperature furnace TMAX = 1750°C
- Vacuum and atmospheric plasma generator
Numerical simulations are used in addition to the experimental investigation, by means of various commercial and open source simulation codes.
2023
Influence of Non-Thermal Plasma Treatment on Structural Network Attributes of Wheat Flour and Respective Dough
In: Foods 12 (2023), Article No.: 2056
ISSN: 2304-8158
DOI: 10.3390/foods12102056
, , , , , :
Numerical and experimental investigation of irradiance profiles on suspended particles in a flat disk photoreactor for hydrogen generation
In: Chemical Engineering Science 282 (2023), Article No.: 119298
ISSN: 0009-2509
DOI: 10.1016/j.ces.2023.119298
, , , , , , , :
Thermal stability of film forming amines-based corrosion inhibitors in high temperature power plant water solutions
In: Energy Science and Engineering (2023)
ISSN: 2050-0505
DOI: 10.1002/ese3.1625
, , , :
2022
Simulation of a Hydrogen-Air Diffusion Flame under Consideration of Component-Specific Diffusivities
In: Applied Sciences 12 (2022), Article No.: 3138
ISSN: 2076-3417
DOI: 10.3390/app12063138
, , :
Hollow spheres as inert packed bed from lean to rich combustion in porous media
In: International Journal of Heat and Mass Transfer 195 (2022), Article No.: 123067
ISSN: 0017-9310
DOI: 10.1016/j.ijheatmasstransfer.2022.123067
, , , :
Enhancement of Wheat Flour and Dough Properties by Non-Thermal Plasma Treatment of Wheat Flour
In: Applied Sciences 12 (2022), Article No.: 7997
ISSN: 2076-3417
DOI: 10.3390/app12167997
, , , :
Effectiveness of Non-Thermal Plasma Induced Degradation of Per- and Polyfluoroalkyl Substances from Water
In: Water 14 (2022)
ISSN: 2073-4441
DOI: 10.3390/w14091408
, , , , , :
2021
Effect of Steam Flow Rate and Storage Period of Superhydrophobic-Coated Surfaces on Condensation Heat Flux and Wettability
In: Multimodal Technologies and Interaction 9 (2021), Article No.: 1958
ISSN: 2414-4088
DOI: 10.3390/pr9111958
, , , , , , :
2020
Static wettability of differently mechanically treated and amphiphobic-coated aluminium surfaces
In: Materials 13 (2020), Article No.: 2240
ISSN: 1996-1944
DOI: 10.3390/ma13102240
, , , , , :
Role of Individual Heat Transfer Mechanisms Within a Model Baking Oven Heated by Porous Volumetric Ceramic Burners
In: Frontiers in Chemistry 8 (2020), Article No.: 511012
ISSN: 2296-2646
DOI: 10.3389/fchem.2020.511012
, , , :
Evaluation of baking performance by means of mid-infrared imaging
In: Innovative Food Science & Emerging Technologies 61 (2020), Article No.: 102327
ISSN: 1466-8564
DOI: 10.1016/j.ifset.2020.102327
, , , , , :
2019
Investigation of the Concepts to Increase the Dew Point Temperature for Thermal Energy Recovery from Flue Gas, Using Aspen®
In: Energies 12 (2019), Article No.: 1585
ISSN: 1996-1073
DOI: 10.3390/en12091585
, , , , , :
Experimental investigation of the gravity influence on the condensation behaviour on Al and PTFE-samples
27. GALA-Fachtagung "Experimentelle Strömungsmechanik" (Erlangen, 3. September 2019 - 5. September 2019)
In: A. Delgado, B. Gatternig, M. Münsch, B. Ruck, A. Leder (ed.): Proceedings der 27. GALA-Fachtagung "Experimentelle Strömungsmechanik" 2019
, , , , :
Numerical study of the methane-air combustion in the direct-flow burner of the boiler 300 MW TGMP-314 boiler
2nd International Conference on Fusion Energy and Plasma Technologies, ICFEPT 2019 (Moscow, 7. October 2019 - 9. October 2019)
In: Journal of Physics: Conference Series 2019
DOI: 10.1088/1742-6596/1370/1/012006
, , , :
Neuartiges Ofenkonzept
In: brot+backwaren (2019), p. 40-45
ISSN: 0172-8180
, :
Novel baking concept based on the Volumetric Ceramic Burners VCB
World Congress on Advances in Nano, Bio, Robotics, and Energy ANBRE19 (Jeju Island, 17. September 2019 - 21. September 2019)
In: Proceedings of 2019 World Congress on Advances in Nano, Bio, Robotics, and Energy ANBRE19 2019
, :
New oven concept with dominant near-infrared (NIR) thermal radiation heat transfer
In: Cereal Technology [Getreidetechnologie] (2019), p. 40-51
ISSN: 1869-2303
DOI: 10.23789/1869-2303-2019-1
, , :
Impact of non-thermal plasma on the abatement of Perfluorinated compounds present in minute quantities in water effluents
27. GALA-Fachtagung "Experimentelle Strömungsmechanik" (Erlangen, 3. September 2019 - 5. September 2019)
In: A. Delgado, B. Gatternig, M. Münsch, B. Ruck, A. Leder (ed.): Proceedings der 27. GALA-Fachtagung "Experimentelle Strömungsmechanik" 2019
, , , , , , :
Experimental and numerical analysis of the heat transfer in a packed bed exposed to the high thermal radiation flux
In: International Journal of Heat and Mass Transfer 136 (2019), p. 383-392
ISSN: 0017-9310
DOI: 10.1016/j.ijheatmasstransfer.2019.03.009
URL: https://www.sciencedirect.com/science/article/pii/S0017931018357922?via=ihub#!
, , , , , , :
2018
VCB based baking oven concept - efficient, innovative and flexible
In: The Future of Baking: Science-Technique-Technology, Hamburg: f2m foodmultimedia GmbH, 2018, p. 10-17
ISBN: 978-3-9817514-4-4
, :
Degradation of Low Concentrated Perfluorinated Compounds (PFCs) from Water Samples Using Non-Thermal Atmospheric Plasma (NTAP)
In: Energies 11 (2018)
ISSN: 1996-1073
DOI: 10.3390/en11051290
URL: https://www.mdpi.com/1996-1073/11/5/1290/htm
, , , , , , :
Virtual engineering as a base for the novel deck baking oven design
32nd International Conference of European Federation of Food Science and Technology (Nantes, 6. November 2018 - 8. November 2018)
, , , :
Syngas production from waste tires using a hybrid filtration reactor under different gasifier agents
In: Energy Conversion and Management 172 (2018), p. 281-390
ISSN: 0196-8904
DOI: 10.1016/j.enconman.2018.07.046
, , , , , , :
2017
Energieeffizientes Backen mittels innovativer VKB-Technologie: Vom Hartgebäck bis zum Weißbrot
FEI-Jahrestagung 2017 - Industrielle Gemeinschaftsforschung als Katalysator des innovativen Mittelstands (Bonn, 4. September 2017 - 6. September 2017)
DOI: 10.13140/RG.2.2.27374.10561
URL: http://www.fei-bonn.de/veranstaltungen-termine/jahrestagungen/jahrestagung-2017
, , , , , :
Combustion of solid fuel in a hybrid porous reactor
In: Energy Procedia 120 (2017), p. 431-438
ISSN: 1876-6102
DOI: 10.1016/j.egypro.2017.07.202
, , , , , :
Experimental Investigation of Solid Fuel Combustion Process in a Hybrid Porous Reactor
In: Journal of Energy and Power Engineering 11 (2017), p. 589-596
ISSN: 1934-8975
DOI: 10.17265/1934-8975/2017.09.004
URL: https://www.davidpublisher.com/Public/uploads/Contribute/59cc53e9610bc.pdf
, , , , :
Cleaning of the surfaces in the food industry using cold plasma
25. GALA-Fachtagung "Experimentelle Strömungsmechanik" (Karlsruhe, 5. September 2018 - 7. September 2018)
In: Ruck, Bodo; Gromke, Christop ; Leder, Alfred; Dopheide, Dietrich (ed.): Proceedings der 25. GALA-Fachtagung "Experimentelle Strömungsmechanik", Karlsruhe: 2017
, , , , :
Application of the porous Volumetric Ceramic Burner for Bread Baking in a Deck Baking Station
XXIII internationales Symposium "Research-Education-Technology" (Stralsund, 12. October 2016 - 13. February 2019)
In: Proceedings of 23rd International Symposium, Research-Education-Technology (RET) 2017
, , , , :
Development and evaluation of the novel baking concept based on a highly radiative volumetric ceramic burner (VCB)
FEI Jahrestagung 2017 - Industrielle Gemeinschaftsforschung als Katalysator des innovativen Mittelstands (Bonn, 4. September 2017 - 6. September 2019)
DOI: 10.13140/RG.2.2.15630.05448
, , , , :
Mehr Effizienz - Volumetrische keramische Brenner - eine innovative, energieeffiziente Technologie für den Backprozess
In: Backtechnik Europe 4 (2017), p. 42-45
ISSN: 2192-824X
, , , , , :
2016
Hydrocarbons conversion to syngas in inert porous media combustion
In: International Journal of Hydrogen Energy Vol. I (2016), p. 5867-5864
ISSN: 0360-3199
DOI: 10.1016/j.ijhydene.2016.02.065
URL: http://www.sciencedirect.com/science/article/pii/S036031991531541X?via=ihub
, , , , :
2015
Influence of the Inter-structural Gap between the Combustion Zone and the Flame Trap on the Properties of the dual Layer Porous Burners in Operation
7th European Combustion Meeting (Budapest)
In: Proceedings of the 7th European Combustion Meeting 2015
, , , , :
Comparison of the operational characteristics of the commercially available and newly developed porous burner flame traps for high temperature applications
27. Deutscher Flammentag - Verbrennung und Feuerung (Clausthal-Zellerfeld)
In: Verbrennung und Feuerung : 27. Deutscher Flammentag, Düsseldorf: 2015
, , , , :
Overview of experimental evaluation of innovative non-thermal plasma treatment of biotic and abiotic matter
International Nonthermal Processing Workshop (Athen)
In: Proceedings of the International Nonthermal Processing Workshop 2015
, , , , , , :
Investigation of advanced temperature and thermo shock resistant ceramic components for high temperature porous burners
European Conference on Industrial Furnaces and Boilers (INFUB) (Gaia (Portugal))
In: Proceedings of the 10th European conference on industrial furnace and boilers 2015
URL: https://www.researchgate.net/publication/280881956_Investigation_of_advanced_temperature_and_thermo_shock_resistant_ceramic_components_for_high_temperature_porous_burners
, , , , , , , :
Numerical simulation of interfacial closures for 3D bubble column flows
In: Chemical Engineering & Technology 38 (2015), p. 777-786
ISSN: 0930-7516
DOI: 10.1002/ceat.201400182
URL: http://onlinelibrary.wiley.com/doi/10.1002/ceat.201400182/pdf
, , :
Characterization of the heat transfer within the baking oven based on the volumetric ceramic burner (VCB) technology
29th EFFoST Conference - Food Science Research and Innovation: Delivering sustainable solutions to the global economy and society (Athen)
In: 29th EFFoST Conference Proceedings - Food Science Research and Innovation: Delivering sustainable solutions to the global economy and society 2015
, , , :
2014
Spektroskopische Untersuchung und Charakterisierung der Nah-Infrarot (NIR) Strahlung eines volumetrischen keramischen Porenbrenners
Lasermethoden in der Strömungsmesstechnik (Karlsruhe)
In: Proceedings der 22. GALA-Fachtagung "Lasermethoden in der Strömungsmesstechnik" 2014
, , , :
Bildung, Verhalten und Lebensdauer von Plasmabullets in einem kalten Plasmastrahl bei Atmosphärendruck
Lasermethoden in der Strömungsmesstechnik (Karlsruhe)
In: Proceedings der 22. GALA-Fachtagung "Lasermethoden in der Strömungsmesstechnik" 2014
, , :
Numerical analysis of heat transfer characteristics in energy piles
In: Proceedings in Applied Mathematics and Mechanics 14 (2014), p. 757-758
ISSN: 1617-7061
DOI: 10.1002/pamm.201410361
URL: http://onlinelibrary.wiley.com/doi/10.1002/pamm.201410361/pdf
, , , , , :
2013
Untersuchungen zur Vergasung von Biomasse mit nicht-thermischem Stickstoff Plasma
26. Deutscher Flammentag (Duisburg)
In: VDI-Berichte: 26. Deutscher Flammentag "Verbrennung und Feuerung", Düsseldorf: 2013
, , , :
Experimentelle Untersuchungen zur Vergasung von Biomasse mit nicht-thermischem Stickstoff Plasma
Lasermethoden in der Strömungsmesstechnik (München, 3. September 2013 - 5. September 2013)
In: Deutsche Gesellschaft für Laser-Anemometrie GALA e.V. (ed.): Proceedings der 21. GALA-Fachtagung "Lasermethoden in der Strömungsmesstechnik" 2013
, , , :
Optimization of inlet mixture quality by means of third gas for regenerative porous burners with highly preheated air
European Combustion Meeting (ECM 2013) (Lund, Schweden)
In: Proceedings of the 6th European Combustion Meeting (ECM 6) 2013
, , , , , :
2011
Gasification of jordanian oil shale using a nitrogen non-thermal plasma
31st Oil Shale Symposium (Golden, Colorado (USA))
In: Proceedings of 31st Oil Shale Symposium 2011
, , , :
Development and testing of a new concept for regenerative porous burner with preheated air
9th European conference on industrial furnaces and boilers (Estoril, Portugal)
In: Proceedings of the 9th European conference on industrial furnaces and boilers, Estoril, Portugal: 2011
, , , , :
Optimization of Fuel Inlet Configuration for Porous Burners with Preheated Air
European Combustion Meeting (Cardiff)
In: Proceedings of the European Combustion Meeting 2011 2011
, , , , :
2010
Experimental Results of Long Time Tests of Porous Burners with Ceramic Housing for High Temperature Application in Glass Industry
High temperatures ceramic materials and composites : 7th International Conference on High Temperature Ceramic Matrix Composites (HT-CMC 7) (Bayreuth)
In: High temperatures ceramic materials and composites : Proceedings 7th International Conference on High Temperature Ceramic Matrix Composites (HT-CMC 7), Berlin: 2010
, , , , :